How to Conduct an Inventory Audit for Your E-commerce Business
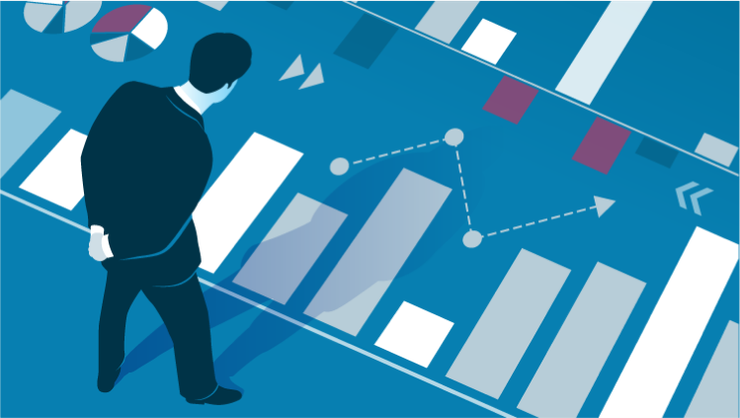
As an e-commerce retailer, inventory is the lifeblood of your company. When you manage inventory efficiently, it’s easy to pick, pack, and ship orders without incident. However, when inventory problems arise, your customers will notice, which can spell trouble for your business.
Luckily, there’s an easy way to combat them: conducting an inventory audit. Keep reading to find out what an inventory audit is and how to conduct one.
What Is an Inventory Audit?
An inventory audit is a process that ensures a company’s inventory and financial records match. Auditing inventory can be done by employees or you can hire third-party service professionals to complete them.
While physical inventory counting involves going through each item in the warehouse and counting, inventory audits take it a step further by documenting not only the quantity of product on the shelf but also the quality and condition. Inventory auditing also helps companies identify occurrences of theft, misplacement, or damage.
Why It’s Important to Audit Inventory
Auditing inventory is important because it helps companies find and eliminate inventory problems. In short, they are instrumental in making important business decisions that can help you elevate your business to meet customer demands, adapt to changes in the supply chain, and ensure your money is being spent most efficiently.
Let’s take a closer look.
Identify and Solve Inventory Problems
Although inventory management software can help you keep track of products in your warehouse, it doesn’t always track goods in transit to or from your fulfillment center. In other words, inventory auditing gives you a more complete picture of your inventory, which enables you to find and fix smaller issues before they cause significant problems.
For example, let’s say you’re trying to prepare your business for the rush of orders to come in the holiday season. By conducting an inventory audit early in the process, you’ll know exactly how much additional inventory to order from your suppliers. This means you can avoid going out-of-stock and missing out on orders and avoid going overstock and having to sell your products at lower price than anticipated and cutting into your margins.
Inventory auditing is also a great tool for e-commerce businesses to use before implementing inventory management software for the first time since it eliminates any errors in the system.
Ensure Inventory Software and Process Accuracy
Performing regular inventory audit procedures can help business owners craft and execute daily operations that champion good inventory management. With inventory auditing, you can find and fix inventory management processes that might be wreaking havoc on your inventory and financial records.
This is especially true when you have new people working with a new inventory management software. The technical set up is open to human error and without conducting a successful audit, you might have managers taking the wrong inventory management strategy.
Data Collection
Poor inventory management can result in missed sales, unstable cash flow, and disappointed customers. Performing regular inventory audits can help you better forecast your customers’ demand. That means you’ll have fewer problems with backorders or tying cash flow up in inventory that doesn’t sell.
You can also study the seasonality of your business to find when your customers are most willing buy and when. This allows your business to be better prepared year over year.
How Often Should You Conduct an Inventory Audit?
Performing inventory audit procedures at regular intervals will indeed benefit your business. But how often should you conduct one? The answer depends on your warehouse size and company needs.
At a minimum, you should conduct an inventory audit once or twice a year, preferably near the end of a financial reporting period. However, performing more regular inventory audits can lead to better visibility. Conducting an inventory audit once every quarter allows you to best keep track of the seasonality of your business.
Common Inventory Audit Procedures
When it comes to inventory audit procedures, there is no one-size-fits-all approach. Luckily, there’s no shortage of approaches to choose from.
Here are nine of the most effective inventory audit procedures:
Physical Count
Performing a full physical count is one of the most popular ways to conduct an inventory audit. This approach involves counting each piece of inventory in the warehouse and recording your findings.
Cutoff Analysis
A cutoff analysis involves shutting down all warehouse operations while an inventory audit is in progress. During this time, no inventory is received, packed, picked, or shipped. While this allows inventory auditing to be more accurate, it does disrupt normal daily warehouse activity.
Finished Goods
When inventory completes the production process, it is called a “finished good.” Finished goods inventory analysis involves calculating the inventory value of a shipment and ensuring those numbers match financial statements.
Freight Cost Analysis
Freight cost analysis involves examining freight costs and instances of shipments getting lost or damaged in transit. This allows you to include freight costs as a part of your overall inventory cost.
Overhead Analysis
Overhead analysis measures the expenses required to house a business, such as utilities, building rental, and other “hidden” costs. By performing an overhead analysis, you can better factor these items into inventory costs.
Inventory in Transit
Inventory in transit audits take into account inventory that is being transferred from one location to another. This ensures that incoming inventory is eliminated from one database and transferred to the correct one.
High-value Stock Tests
High-value stock tests, or ABC analysis, perform audits by classifying inventory into different categories according to their profitability. These categories are called Class A (high-value), Class B (mid-tier), and Class C (low-value). This analysis lets you strategically place inventory throughout the warehouse to streamline picking and packing procedures.
Direct Labor Analysis
“Direct labor” refers to the cost of labor required to produce a product. This type of analysis includes costs associated with things like hourly wages, overtime, and shift differential pay. Keeping track of these costs allows business owners to more accurately include them in their overall inventory cost.
Inventory Count Reconciliation
Inventory count reconciliation involves ensuring the physical inventory account in the warehouse matches the numbers in the database. This ensures that products are not over or undersold and can eliminate pesky problems, like backorders.
How to Conduct an Inventory Audit
Though conducting an inventory audit might sound intimidating, it’s simpler than you think. It can be completed in just seven simple steps:
Step One: Identify items
First, you’ll need to decide what inventory will be included in your audit. For example, you might choose to complete a physical count of all inventory. Alternatively, you may choose to prioritize certain inventories based on their value or risk.
Step Two: Schedule Audit
Planning is essential to a successful inventory audit. A good rule of thumb is to schedule audit procedures at a time that is the least disruptive to daily operations. For many e-commerce businesses, that means overnight.
Step Three: Collect Documents
Collecting all documents necessary for an inventory audit ensures procedures are completed accurately and efficiently.
Step Four: Conduct the Audit
After deciding which inventory audit procedure is best for you, it’s time to conduct the audit. Make sure to use an unbiased auditor that has plenty of experience in the field to yield the most accurate results.
Step Five: Record the Findings
Recording audit findings gives you the data you need to improve operational processes.
Step Six: Report Findings
After audit completion, create a report that includes the findings. This better enables you to compare the current audit to past and future audits, which gives you a more complete vision of where your business has been and where it’s headed.
Step Seven: Keep Historical Records
Keeping historical records gives you a point of reference to compare to in the future. Consequently, it’s always a good idea to keep your findings archived for future use in the event that you have new managers looking to conduct an audit.
Inventory Auditing Best Practices
Choosing the right auditing strategy and getting prepared are two easy things you can do to improve the results of your audit. It’s also a good idea to keep a well-organized warehouse, which makes the entire audit process go smoothly.
A few more inventory auditing best practices include:
- Using teams to count the same inventory twice
- Using technology like scanners to reduce human error
- Using SKUs or UPCs to track inventory
- Working with a professional auditor
Overall, conducting an inventory audit can help you keep accurate stock records and financial reporting while helping you prepare for demand in the future. Once complete, using a tool like Shippo ensures that all of the hard work you put into your inventory audit translates into stress-free shipments to your customers and further business growth. Get started today!