Modern Warehouses: Current and Future Trends
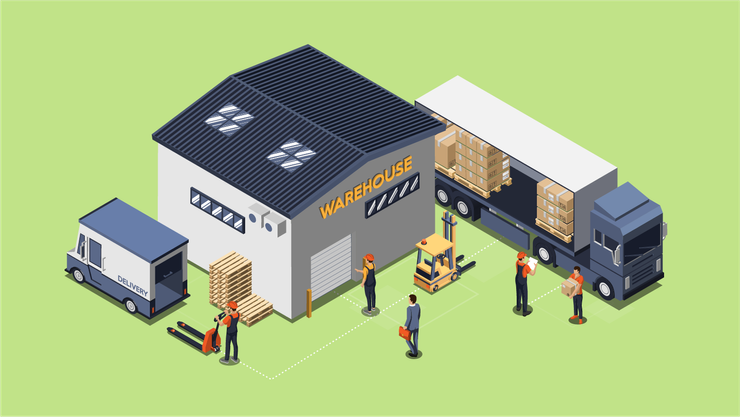
Shippo Snippets:
- Speculation exists about the future of warehouses, including the evolving role of human contributions
- With machine learning, workers are provided the most efficient pathways to fulfill multiple orders
- Going vertical and underground? Warehouses of the future may look quite different from those operating today
The Story:
As more and more consumers continue to patronize online businesses, the logistical foundation that supports the entire operation has also been evolving. And with anything involving developing technology, it’s easy to jump to conclusions of what that might eventually look like. Will robots become commonplace? How will warehouses be structured as the world gets even more urban? Either way, COVID-19 has shown us that without a strong and flexible supply chain in place to facilitate the increase in demand, many people would go without vital items.
Well, as some seemingly “futuristic” developments are already happening, one big question continually comes to mind as things evolve: will many or most tasks be automated with no humans involved? Amazon’s then Director of Robotics Fulfillment, Scott Anderson stated last year that a fully automated warehouse at his company is at least a decade away. Statements like that do imply that humans are very much needed to keep the ship afloat right now. But, other developments have been afoot that contradict the timing.
One fully automated warehouse has already been prototyped by the startup company, Mujin, and debuted at a technology show in Tokyo. When Mujin’s robotics technology was then put into practice for e-commerce giant JD.com in Shanghai, China, they had only a few employees, rather than the hundreds that typically might be needed for a warehouse of that size. Their job? To service machines.
This 40,000 square foot warehouse in Shanghai has several industrial robots involved in picking, transferring, and packing, along with Mujin robot controllers, merchandising-carting robots, and more. Mujin would like to implement this technology in the United States, with the goal of pushing standardized automation forward.
So, it’s pretty clear that warehouse jobs will continue to evolve. Fewer people will need to do the physical labor, but people will still be needed to monitor and manage warehouse operations, and to create and refine technologies. Even when much of it can be done remotely, people with expertise will still need to travel to the warehouse to address problems and make repairs.
Warehousing in the 20th Century
The earliest warehouses date back as far as Ancient Rome. Relying on brute strength and authority, if you wanted your warehouse to become more efficient, the only practical answer was for workers to work faster and harder.
Fast-forwarding by about 9,000 years, workers in warehouses were still spending about half of their time on paperwork in the 19th century, with manual data entry often causing errors in orders. Few things can damage a company’s reputation more than when word gets around that they don’t fulfill orders correctly, so it’s not surprising that warehousing companies sought out better technologies for their fulfillment centers.
In the 1950s, automated guided vehicles could navigate warehouses without the need for drivers or fixed rails. By the 60s? Automated storage and retrieval systems were put into play, with this computer-controlled technology storing and retrieving what was needed. This could be considered the beginning of modern warehousing.
Modern Warehousing in the 21st Century
Technology continues to drive warehousing forward, with a wide range that enables warehouse workers to become more efficient and productive while also reducing picking and shipping errors. In fact, according to a 2020 Study, 74% of warehouses are now providing staff with moderate to advanced technology, with these three types being the most common:
- Internet of Things (IoT): 72%
- Tablet computers: 72%
- Barcode scanning: 70%
For the unfamiliar, IoTs are, at their simplest, objects or things in the world that are connected to the internet. They are valued for their ability to receive or send information—or, sometimes, both. A common example of an IoT that receives information is a sensor. A sensor could monitor light, temperature, or motion, as just three examples. That same sensor, if sophisticated enough, could also send information, perhaps to turn down the temperature in an overheated piece of equipment, all through a network.
In a warehouse, IoTs can provide users with real-time data that can be analyzed and used to accurately manage inventory, something even more crucial with the increasing numbers of e-commerce orders in 2020. Companies need to know, in real-time, whether an item is or isn’t in stock to meet customer demand so they can provide accurate information and quality service to them.
Vision picking smart glasses are a good example of innovative usage of IoT in warehouses. The team can work hands-free, with augmented reality (AR) feeding workers with relevant information. Productivity has seen increases by 15% on average, as warehouse employees can ergonomically see picking instructions and warehouse locations through these glasses, and are then guided to accurately fill orders. These vision picking devices also direct where items should be placed on a cart and so forth, from a start to finish AR experience.
As another example of IoT in the warehouse, autonomous mobile robots (AMR) use sensors and cameras to navigate in a way that doesn’t need predetermined paths. Instead, this technology senses its surroundings and its placement within the environment. They can move shelving, deliver bays to pickers, work alongside warehouse employees, validate items picked, and much more.
Here’s more about another kind of commonly used technology in modern warehousing: barcode scanners. These collect info about what comes in and out of a warehouse, along with its shipping info, while radio-frequency identification technology (RFID) keeps track of where each item is located. That’s a one-two punch to make warehouses more efficient and error-free. These innovations, all by themselves, would make any Roman warehouse worker green with envy, but that’s really just the foundation of today’s technology.
Voice technology is now simple to use and is easily understood, helping with order management, inventory, and more. Plus, warehouse management software can transfer information between computers for even greater warehouse efficiency.
Then comes the next step in modern warehousing technology: machine learning. Although barcode readers, voice technology, and machine communications make a big difference in operations, they’re still only inputs and messages. Machine learning, though, takes warehouses to the next step. When shipments come in, machine learning software scans where items are located and matches the new ones to the right place through artificial intelligence.
It “knows” where to direct the new shipments, giving workers directions so they can get to a location in the fastest way and reducing the number of steps involved in picking orders. Let’s say, for example, that a warehouse contains massive numbers of small parts, ones that look very much alike to the human eye. Machine learning can warn a worker when a mistake might easily be made and can also take a look at previous orders from the customer whose order is being fulfilled, highlighting when a warehouse worker selects items that don’t fit previous patterns.
Without machine learning technology, a worker might decide to fulfill one order at a time to avoid mistakes. With machine learning, though, workers are provided the most efficient pathways to fulfill multiple orders while also separating orders to prevent errors.
Machine learning can also proactively see where delays could happen, and warn you of products that may expire soon, suggest what products just aren’t moving well anymore, and much more.
What Does the Future Hold?
Warehouse changes are happening at a rapid pace. In fact, in China, warehouses are one of the economy’s fastest-growing segments, with autonomous robots able to accurately sort 18,000 parcels hourly. So, what can be expected in the United States? One thing we know for certain is that consumers will continue to expect and anticipate faster deliveries of their items, no matter where they reside, and in general, the world will continue to become more urban.
So, what will that mean for tomorrow’s warehousing? Logic dictates that warehouses will need to move closer to the customers they serve, geographically speaking, to provide the lightning-fast delivery service that customers will demand. The problem? Limited urban space and higher real estate costs in those areas. This will mean that warehouses may need to become:
- More compact with more limited inventory
- Supplemented with 3D printing to print needed items on demand
- More reliant upon highly accurate predictive analytics (with less space for inventory, there’s even less room for error)
And it’s these space limitations that will likely lead to a shared service warehousing system. In other words, numerous companies will share space that’s armed with the latest in technology—with the ability to allow small businesses to take more advantage of the advancements that will be available to companies with bigger pockets. Major carriers will be positioned nearby under this scenario, to provide same-day delivery or curbside pickup.
Keeping that limited warehouse space in mind, when they need to expand, horizontal growth may not be possible—and that’s why these structures may extend up into the sky, with drone delivery being used. Here’s how China’s largest online retailer JD.com—one with more than 300 million customers, and one that already does plenty of same-day deliveries—envisions warehouses of the future. They are vertical, with underground delivery systems.
As another solution for warehouse space in crowded urban areas, warehouse technologies could be installed in the back areas of retail stores and/or in vacant strip plazas in geographies of choice.
This may well be the impetus for more manufacturers and wholesalers to stop their drop-ship arrangements to take advantage of the value in shipping directly to consumers. This is already happening, and the DTC movement may well continue as e-commerce businesses and other companies look for ways to satisfy customers while improving profit margins.
Adding Green to the Equation
As Millennials and Gen Zs continue to move into decision-making positions and grow even further in their influence, it’s likely that the demand for green logistics will continue to grow.
As far as warehouses themselves, this is already being seen in energy-efficient systems, from solar panels to LED lighting, green materials to skylights allowing for natural light, cool-roof systems, and more. This will also include further advancements in sourcing from eco-friendly partners, reusing and recycling packaging materials, lowering transportation-related energy consumption, and more.
Shippo is here to help you optimize your shipping operations, while saving you time and money in the process.
Looking for a multi-carrier shipping platform?
With Shippo, shipping is as easy as it should be.
- Pre-built integrations into shopping carts like Magento, Shopify, Amazon, eBay, and others.
- Support for dozens of carriers including USPS, FedEx, UPS, and DHL.
- Speed through your shipping with automations, bulk label purchase, and more.
- Shipping Insurance: Insure your packages at an affordable cost.
- Shipping API for building your own shipping solution.
Stay in touch with the latest insights
Be the first to get the latest product releases, expert tips, and industry news to help you save time and money on shipping.