#1 Picking and Packing Mistake Small Businesses are Making
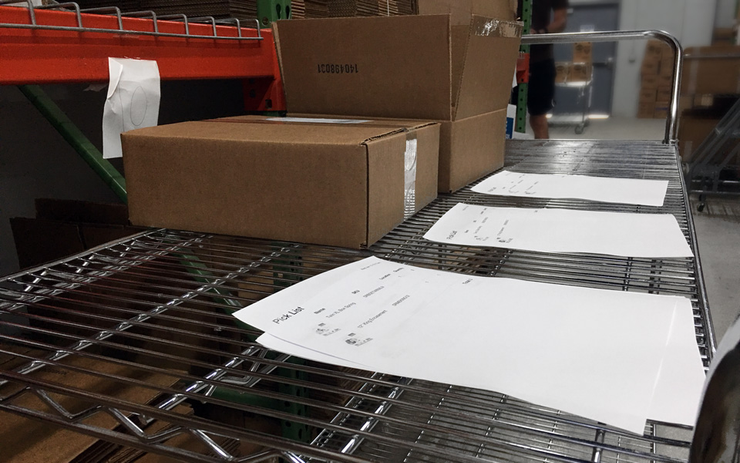
When it’s time to pick and ship e-commerce orders, most small businesses tend to follow the same routine. The fulfillment process usually involves printing out paper pick lists for each order, picking items for one order at a time, packing and shipping that order, then moving on to the next pick list on the printed stack.
This routine is called discrete picking and shipping, and is the most common fulfillment method among online retailers. While discrete fulfillment is straightforward and easy to adopt, that simplicity comes at a major cost in fulfillment efficiency. You could be picking and shipping your orders much more quickly and accurately, leaving you with more time to run other parts of your business.
Discrete fulfillment, your worst picking and packing enemy
Discrete fulfillment processes are light on “process” — that’s why so many small businesses get by just fine using it. All you have to do is get a list of items needed for an order, head over to your store, and start picking the items. The items go in a box, you type up some shipment settings, and print out a label.
However, this simplicity can affect how quickly you are fulfilling your orders. Since you are only picking one order at a time, you’ll find yourself walking to the same items or sections of your store several times in a day. For example, if one item is part of 20 orders in a day’s queue, then a discrete picker would be walking to that item’s location, picking it, then moving on to the next item 20 times that day. Similarly, that item might be packed and shipped the exact same way 20 different times, requiring the worker to type out nearly the same shipment info and wait for a label to print every time.
The travel time between items in a store isn’t something a lot of small business owners worry about. It’s understandable — you probably have bigger fish to fry. It’s common for a worker to simply start from the top of a picking list and work their way down to the bottom. In that process, the picker might be passing items that they need, only to return to that item later on. These sort of small efficiency gaps can add up to a sizable (and costly) expense in time and labor.
What’s most unfortunate about this lack of order fulfillment efficiency is that it comes with no benefit to the accuracy of the order. Even though the picker’s attention is focused on a single order, there is likely nothing in the process that helps to ensure that the items are being picked correctly, or that the shipment is processed correctly. Businesses tend to simply expect the worker to double-check their work, and this can lead to an expensive amount of picking and shipping mistakes. Any accuracy from this, whether high or low, is incidental at best, and can be carried over to a more efficient order fulfillment method.
Save time and headaches with batch fulfillment
The adoption of batch picking and shipping often comes from store owners frustrated with the errors and inefficiencies of their old fulfillment routine. Research in fulfillment clearly shows batch fulfillment to be more efficient, much faster per order, and even more accurate.
The basic batch fulfillment workflow is simple. Instead of starting with one order, a store worker will group similar orders together in batches. These orders are matched due to the items they may have in common or how close together their items are on the picking floor. Organizing your store or warehouse into zones will help with deciding how to group orders into batches.
Once the batches for the day have been arranged, a picker will start on a batch by setting up a cart or table with bins for each order in the batch. Ideally, a picking cart would be easy to maneuver around the store so that the picker can bring the orders with them.
With their picking cart and order bins set up, a picker can now move through the store and pick the items needed to fill the orders. If one item is needed for many orders in the batch, the picker will grab as many of that item as they need for the entire batch in a single visit. This significantly reduces the number of steps needed to complete picking the orders, and will lead to the orders being fulfilled in a fraction of the time.
Once each order in the batch has been picked, all the shipping labels for the batch can be processed at the same time. With smart sorting, batches can be organized so that they have similar shipping methods or package dimensions, making it easier to print the labels out as quickly as possible. Once each order in the batch has been picked, packed, and shipped, it’s time to get started on the next batch.
Kick your order fulfillment into high gear
By switching to batch fulfillment, you’re already taking a big step in making your order processing more efficient and cost-effective. But there are many more small optimizations you can make to speed things up:
For starters, group single-item orders together as often as possible. These “singles” are the biggest offenders when it comes to fulfillment efficiency: they may be faster to pick, but they usually take just as much time to pack and ship as larger orders. To address that shortcoming, group orders asking for the same single item together into batches. This way, you can pick the entire batch in one step, and the shipping settings for each order will be nearly identical since they’ll have the same weight, dimensions, and values.
When you’re sorting batches that contain multi-item orders, make an effort to keep the amount of zones per batch as low as possible. If the items in a batch are closer together, they’ll take less time to pick. A batch that takes a worker around the entire picking floor can eat up a lot of time.
Larger operations that handle high daily order volume may need to invest in specialized warehouse fulfillment equipment to make the most out of a batch workflow. Things like slotted picking carts, bin lights, and zone-to-zone conveyor systems can further reduce the time and effort spent per order.
This post is brought to you by Josh Barnett at SKULabs, the multi-channel inventory, barcode, and order fulfillment solution. With SKULabs, you can start batch picking and shipping with any computer or mobile device that’s connected to a barcode scanner. SKULabs is an all-in-one solution designed from the ground up for batch fulfillment, and is also fully integrated with Shippo — simply add your Shippo account to start picking faster than ever.
Shippo is a multi-carrier API and web app that helps retailers, marketplaces and platforms connect to a global network of carriers. Businesses use Shippo to get real-time rates, print labels, automate international paperwork, track packages and facilitate returns. Shippo provides the tools to help businesses succeed through shipping.
Looking for a multi-carrier shipping platform?
With Shippo, shipping is as easy as it should be.
- Pre-built integrations into shopping carts like Magento, Shopify, Amazon, eBay, and others.
- Support for dozens of carriers including USPS, FedEx, UPS, and DHL.
- Speed through your shipping with automations, bulk label purchase, and more.
- Shipping Insurance: Insure your packages at an affordable cost.
- Shipping API for building your own shipping solution.
Stay in touch with the latest insights
Be the first to get the latest product releases, expert tips, and industry news to help you save time and money on shipping.